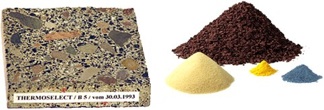
La technologie Thermoselect transforme 100% des déchets de toutes sortes en gaz de synthèse et en matière première réutilisable par l’industrie.
Ici, des granules utilisés dans la construction, du fer-nickel, du zinc, du sel et du souffre.
100% des déchets sont recyclé à 100% sans pollution ou enfouissement.
|
Le procédé Thermoselect
Seules les matières non recyclées et non réutilisées seront livrées à l’usine soit les déchets ultimes uniquement. Il s’agit donc d’un équipement stratégique et unique qui vient complémenter les efforts de recyclage et de réutilisation de la région et permettre d’atteindre un taux de 100 % de recyclage, de réutilisation et/ou de revalorisation des matières résiduelles.
Le procédé Thermoselect : Après leur déversement dans les fosses de réception de l’usine par les camions de collecte, les déchets sont acheminés vers l’unité de gazéification par l’opérateur de grue. Après avoir été compactés pour en retirer le maximum d’air, ils traversent un tube de dégazage étanche qui a pour but de réaliser la combustion des déchets organiques par pyrolyse à 600 oC environ. La chaleur est générée grâce à l’utilisation du gaz de synthèse produit par le procédé lui-même; environ 40 % du contenu énergétique généré par les matières résiduelles telles que livrées est utilisé à cette fin, le reste étant destiné à la réutilisation comme énergie par des clients à l’extérieur du site.
En sortant du tube, les cubes de déchets charbonnés tombent alors dans le réacteur où la gazéification à haute température permet la fonte des matières inorganiques à 2 000 oC.
Les gaz émis et produits dans le réacteur montent vers le haut et sont acheminés vers un système de refroidissement ultra rapide (30 millisecondes, unique à Thermoselect), qui permet d’éviter la reformation des dioxines et furanes fractionnés antérieurement par la haute température du réacteur. Ainsi aucun furane ni dioxine n’est présent au-delà de cette étape du procédé.
Schéma d’un centre Thermoselect de traitement par gazéification à haute température des déchets ultimes
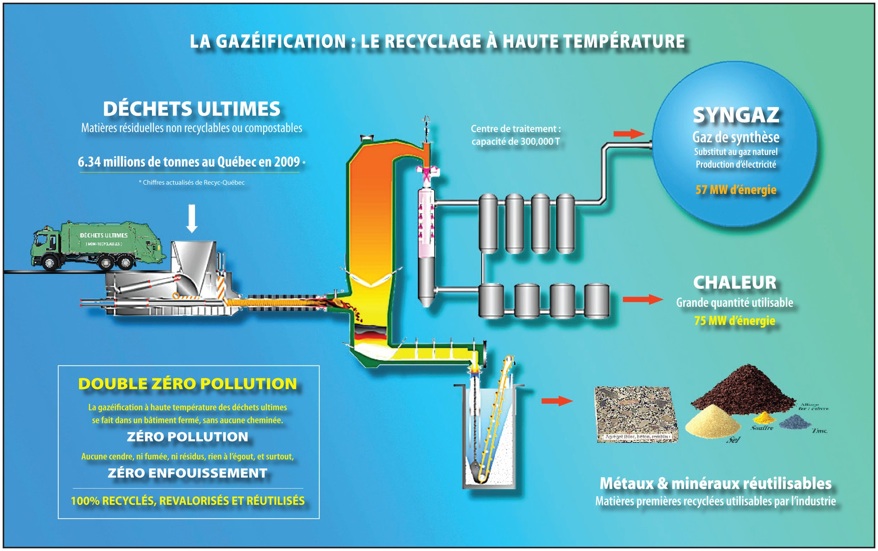
Les gaz résiduels composés de molécules simples, principalement de carbone, d’hydrogène et d’oxygène, sont ensuite traités pour en retirer les substances indésirables comme le chlore. Dans une de ces unités de traitement, du sodium est introduit dans l’eau de refroidissement et la rencontre des gaz chauds avec l’eau froide précipite les solides alors que l’eau s’évapore sous l’effet de la chaleur. Dans cette précipitation chimique, le chlore s’unit au sodium et apparaît sous forme de sel au moment de l’évaporation de l’eau sous l’effet de la chaleur. Le processus de traitement des gaz se poursuit et permet en fin de course d’obtenir un gaz de synthèse réutilisable tel quel par un utilisateur-client externe à l’usine.
Tel que mentionné ci-haut, la transformation des matières présentes dans les déchets non consumés par la première étape, la pyrolyse, est réalisée à très haute température, soit environ 2 000 oC. En plus de la fraction gazeuse dont nous venons de parler, les matières inorganiques solides renferment également des métaux et du verre qui sont fondus à cause de cette très haute température. Le refroidissement subit des solides les transforment en deux produits différents; les métaux se solidifient sous forme de petites boulettes de métal alors que les autres matériaux se figent sous forme de granulés vitrifies inertes. Les métaux peuvent être séparés par l’industrie métallurgique et réutilisés (ex : Noranda), et les granulés vitrifiés inertes vers divers usages dont: comme matière première pour la fabrication de béton et dans la composition de l’asphalte et également par les municipalités clientes, pour la réfection des routes, comme abrasif pour l’épandage préventif sur les routes l’hiver et plusieurs autres applications où du béton est requis.
Les trois lignes de production fonctionnent en continu à l’année, à l’exception d’une période d’entretien planifiée de deux semaines par année, en alternance pour chaque ligne. Grâce à cet entretien en alternance, l’usine fonctionnera en tout temps. Le personnel d’entretien est entraîné et exécute son travail en conformité avec toutes les normes de la CSST. Toute l’aire de réception des résidus est fermée et en pression légèrement négative, de sorte qu’il n’y a pas d’air qui s’en échappe vers l’extérieur, confinant de ce fait toutes les odeurs à l’intérieur. L’aire de réception est ventilée selon les normes, et l’air de ventilation est traité et désodorisé avant d’être rejeté à l’extérieur. Il n’y a donc pratiquement pas d’odeurs perceptibles aux limites de la propriété. Par ailleurs, les opérations se déroulant à l’intérieur des bâtiments, il n’y a pratiquement pas de bruit perceptible aux limites de propriété, ni d’attroupement d’oiseaux, ni de résidus légers emportés par le vent.
|